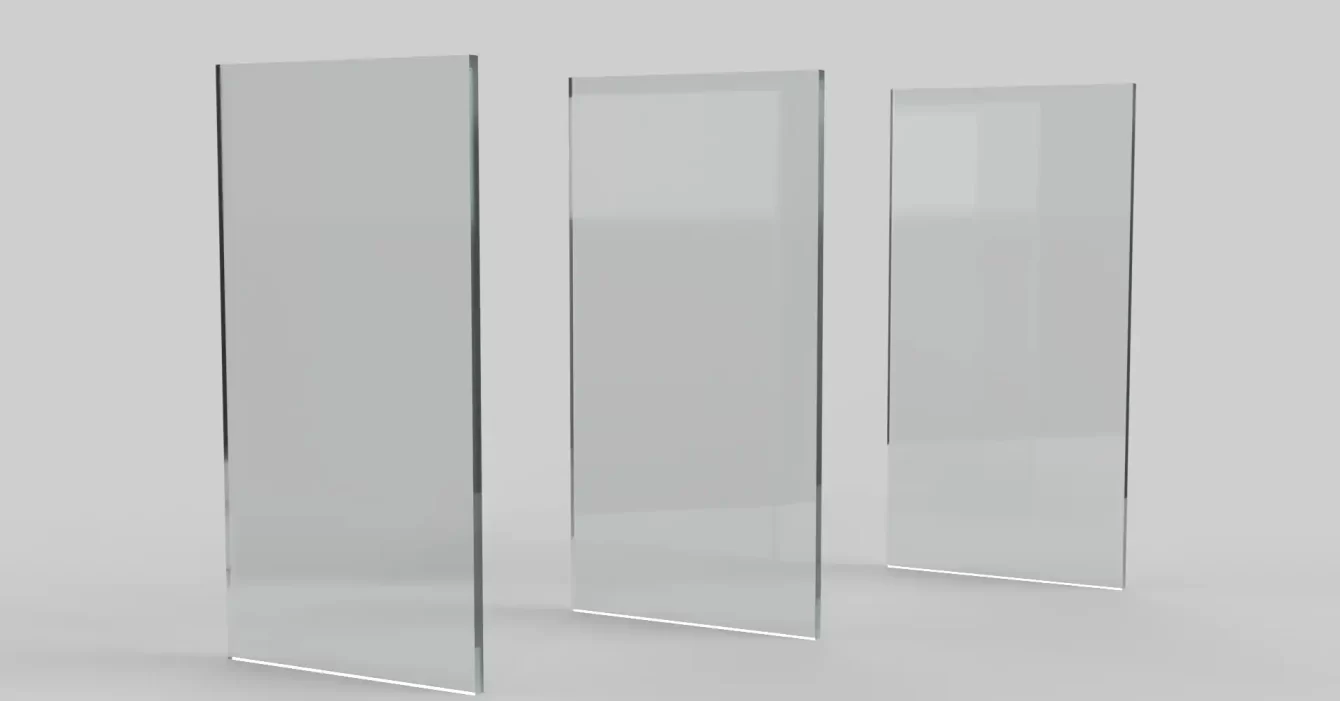
Extrude Sheet
Extrude Sheet description.
Extrusion plate (acrylic plate) has the following properties and use characteristics:
Excellent transparency: Extruded sheet has excellent transparency, almost comparable to glass. This makes it very popular in applications that require transparency, such as display cases, lighting covers, signage, etc.
Good weather resistance: Extrusion plates have good weather resistance and can withstand the effects of UV, moisture and climate change. It does not easily turn yellow, brittle or fade, so it is suitable for outdoor applications, such as outdoor billboards, doors and Windows.
Strength and impact resistance: extrusion plate has good strength and impact resistance, stronger than glass and not easy to break. This makes it widely used in applications that require a high degree of safety and shock resistance, such as protective covers, security Windows, etc.
Light weight and good workability: extrusion plate is lighter than glass, easy to handle and install. It also has excellent machining properties and can be easily cut, drilled, bent and formed for a variety of customized designs and applications.
Flame retardant performance: The extrusion plate can be improved by adding flame retardant to meet specific fire protection requirements. This has led to its widespread adoption in security applications in areas such as construction, electronics and aerospace.
Extruded sheets (acrylic sheets) are suitable for many scenarios and applications, including but not limited to:
- architecture and interior decoration: transparent partition, doors and Windows, ceiling, metope adornment, etc.
- advertising and display: light boxes, billboards, display rack, showcase, etc.
- lighting and optical: lighting, light guide plate, fiber optic transmission, etc.
- and household furniture: eat desk and chair, display cabinets, flower POTS, bathtub, etc.
- auto and transport: Windows, car lamps, traffic signs, etc.
In short, extrusion sheet (acrylic sheet) with its excellent transparency, weather resistance, strength and processing properties, plays an important role in a number of fields and provides a reliable solution for a variety of applications.
Plan and what you might want to know
- If you want to know the scope of the product
- About our arrangements and expectations for the production plan.
- What can we do for you?
Extrude sheet production process
Extrusion plate (acrylic plate) is a common acrylic products, its manufacturing process using extrusion technology.
First, high quality acrylic resin is added as a raw material to the feed port of the extruder. Inside the extruder, the raw material is heated and melted to form a molten substance with a certain viscosity.
The melt is then pushed by the extruder's screw and extruded into continuous plates through the extrusion outlet of the die. The mold shape determines the thickness and width of the final product.
During the extrusion process, the molten material passes through the cooling coiling device and is rapidly cooled into a solid state. In the cooling process, air cooling or water cooling can be used to control the temperature and hardness of the plate.
Once cooled, the sheet is stretched or cut through a traction roller or cutting device to reach the desired size and length.
Finally, after the necessary inspection and quality control, the extrusion plate was judged to be qualified. The inspection items include dimension measurement, appearance inspection, physical performance test, etc.
The extrusion process has the advantages of high efficiency, stability and controllability. It can produce flat, even sheets with good transparency, smoothness and mechanical strength.
Our company is committed to the use of advanced extrusion process, to ensure that the quality and performance of extrusion plate meet the needs of customers. We continue to optimize the process parameters and quality control measures, in order to provide high quality extrusion products to meet the needs of all walks of life.